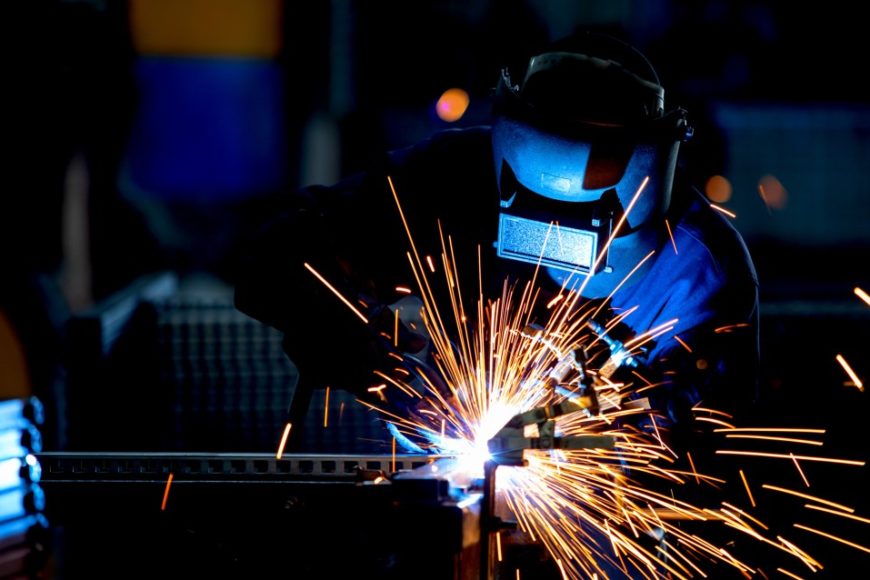
Gas metal arc welding (GMAW) is a joining process that consumes shielding gas in significant volumes. Even hobbyists and other small-scale users of MIG welders require a robust gas delivery system to facilitate their welding process and protect the joint from reacting with atmospheric gases. Contamination of weld joints by ambient gases such as nitrogen (N2) can lead to metal embrittlement and porosity, which can ultimately contribute towards mechanical failure.
In this blog post, Environics outlines the importance of shielding gas delivery systems for welding applications in greater depth.
What is a MIG Welder?
MIG welding is the colloquial term for a gas metal arc welding (GMAW) system. At the heart of the welder is a thin electrode wire that is fed continuously through the torch. The gun generates a current which forms an electrical arc between the tip of the electrode and the workpieces. This arc raises the temperatures of both metals above their melting points, forming a weld pool that fuses the base metals together. Shielding gas is continuously released through the nozzle to blanket this molten joint and protect it from reactants in the atmosphere, including common atmospheric gases and water vapour.
Shielding gas delivery systems typically introduce a gas mixture that includes some combination of argon (Ar) with one or two additional species. Carbon dioxide (CO2), oxygen (O2), and helium (He) are among the most common gases used in conjunction with argon for MIG shielding. These are available in bulk mixtures at distinct ratios to suit joining of distinct metal grades and plates of predefined thicknesses. Premixed gases are generally contained in external pressure containers and are introduced to the welding tool via a pressure regulator.
Shielding Gas Delivery Systems: On-Site Blending
Although premixed shield gas is a quick and easy solution for most MIG welding applications, some dedicated shield gas delivery systems can perform on-site blending for appreciable cost and repeatability benefits.
The Environics Series 3000 Gas Delivery System provides blended gas on demand. It uses precision thermal mass flow controllers (MFCs) to mix two or three gas constituents with an accuracy specification of within 1% of setpoint. This guarantees precise shielding gas mixtures that can be configured for specific joinery projects, with a repeatability of within 0.05% of the full scale. The 3000 is ideal for shops with one or multiple stations being used. The on demand system will provide the required blend without any gain or loss of pressure or flow as additional stations come online or are shut down.
Using premixed gases is costly and sub-optimal for gas conservation. Environics gas delivery systems provide full independence for your MIG welding processes, enabling total control of your gas composition with absolute confidence in the repeatability of your results.
Gas Delivery Systems from Environics
Environics is one of the world’s leading suppliers of gas blending and delivery systems for industrial applications. Our Environics Series 3000 instrument has been successfully used as a gas mixer for applications as varied as welding, medical research, sensor calibration and testing, and modified atmosphere packaging.
If you would like any more information about our gas delivery systems, please do not hesitate to contact us directly.